Prelevigatura, lucidatura e attacco di parti di produzione additiva
Quando si lavora con campioni di produzione additiva, le fasi di preparazione di prelevigatura, lucidatura e attacco variano notevolmente in base al materiale/lega. Ecco brevi consigli per quattro materiali comuni utilizzati in AM.
Titanio In generale, la preparazione dovrebbe seguire i metodi standard utilizzati per altri campioni di titanio.
- A causa della sua elevata duttilità, il titanio è soggetto a deformazioni meccaniche e graffi. La lucidatura diamantata dovrebbe essere evitata, soprattutto per il titanio puro.
- Per il titanio bassolegato, si raccomanda l'elettrolucidatura.
- Per ottenere informazioni più specifiche, è spesso necessario un attacco dopo la preparazione meccanica o elettrolitica. Poiché il titanio è chimicamente resistente, si consigliano reagenti contenenti acido fluoridrico.
- La luce polarizzata è un eccellente metodo d'attacco ottico per il titanio.
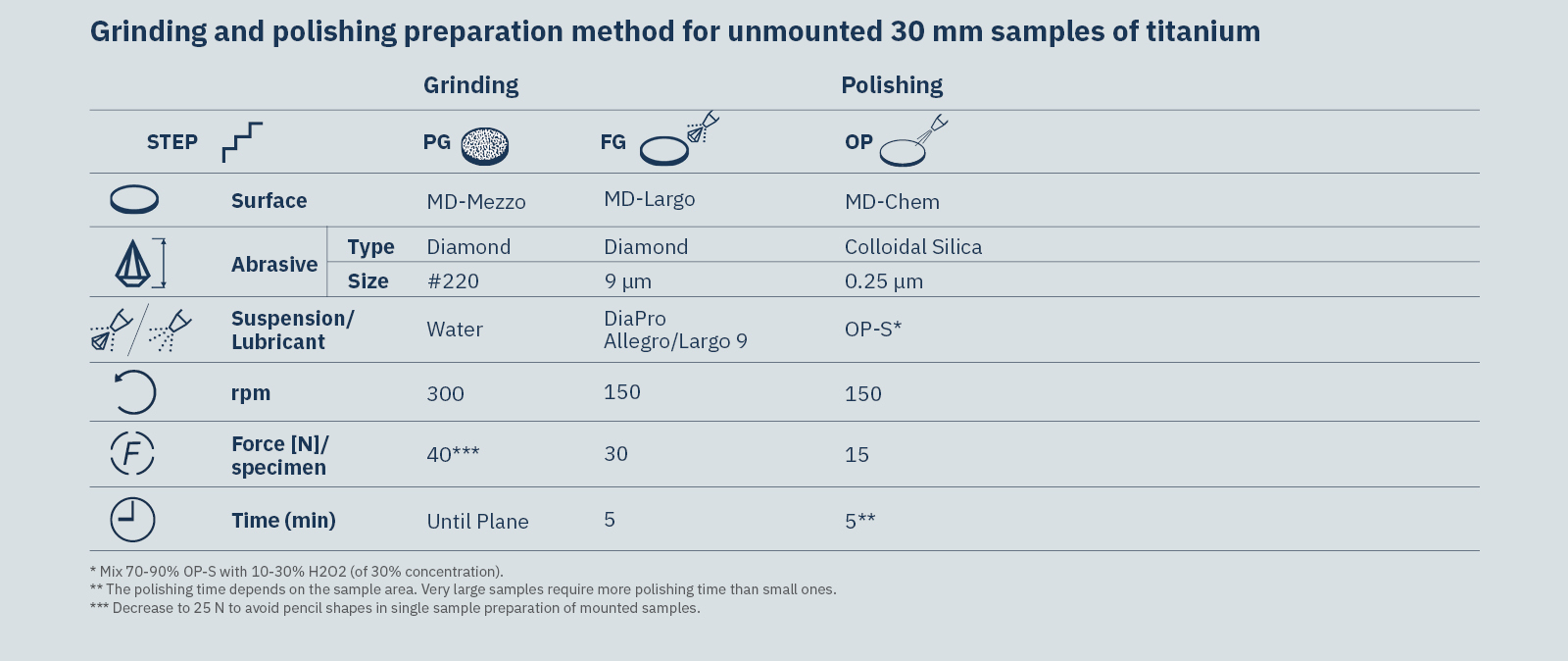
Tabella 2. Metodo di preparazione per la prelevigatura e lucidatura di campioni di titanio da 30 mm. non inglobati.
Per descrizioni dettagliate e metodi collaudati su lucidatura, elettrolucidatura e attacco di campioni di produzione additiva in titanio, consultare la nota applicativa completa.
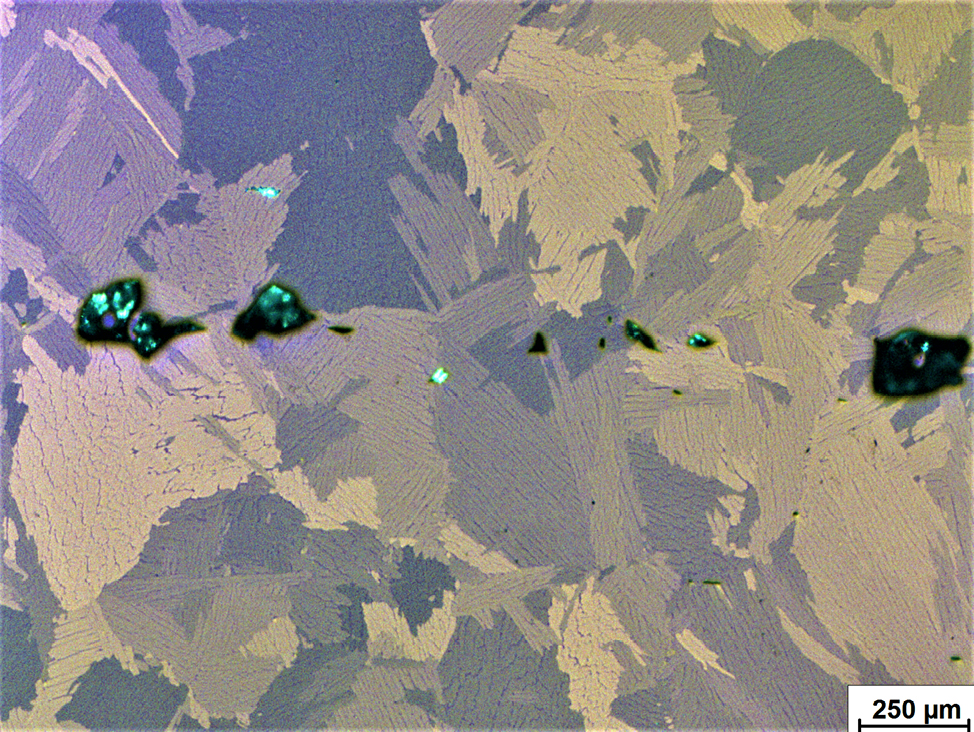
Figura 14. Lucidatura finale del campione in titanio con porosità. Lucidato su MD-Chem con OP-S NonDry e additivo, microstruttura visibile in contrasto di polarizzazione.
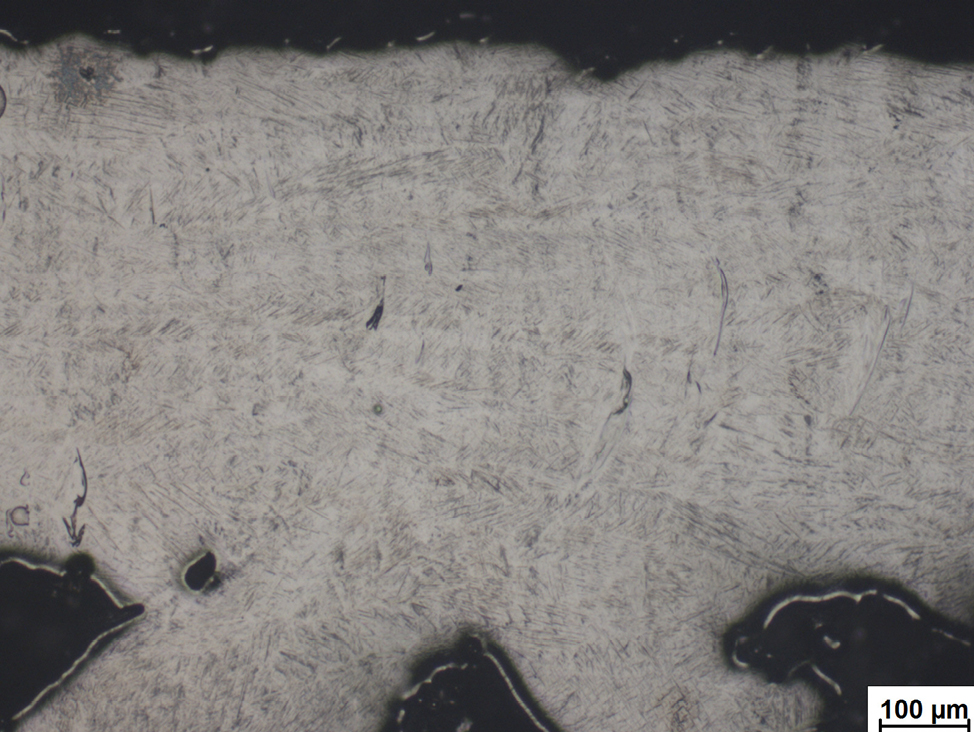
Figura 15. Lega di titanio. Preparazione elettrolitica con A3, non inglobato. Campo luminoso.

Figura 16. Lega di titanio. Lucidata elettroliticamente e attaccata chimicamente con reagente Fuss. Campo luminoso.
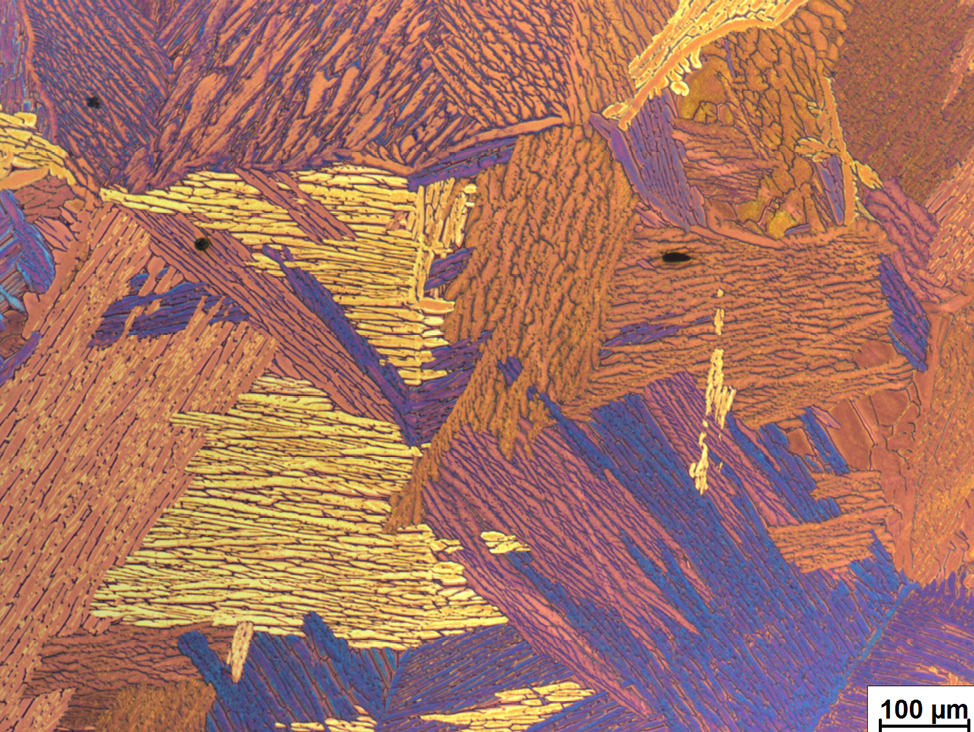
Figura 17. Lega di titanio dopo l'attacco con reagente Keller. Luce polarizzata. Alluminio Sebbene l'alluminio sia un metallo morbido, gli elementi leganti possono modificarne significativamente le proprietà meccaniche. In generale, la preparazione di campioni di produzione additiva dovrebbe seguire i metodi utilizzati per campioni simili in alluminio.
- Per evitare deformazioni, graffi e arrotondamenti dei bordi, si consiglia di utilizzare una superficie di spianatura rigida sviluppata appositamente per le leghe di alluminio, come MD-Molto.
- Per la prelevigatura fine, MD-Largo con sospensione diamantata (come, DiaPro Allegro/Largo) è adatta per molti tipi di alluminio.
- Per ottenere un'accurata lucidatura, far seguire alla prelevigatura fine una fase di lucidatura diamantata (MD-Mol) e una di lucidatura all'ossido (silice colloidale, OP-U).
- Per rivelare ulteriori o specifici dettagli, possono essere utilizzati sia metodi di attacco chimici, elettrochimici e ottici, che una loro combinazione.
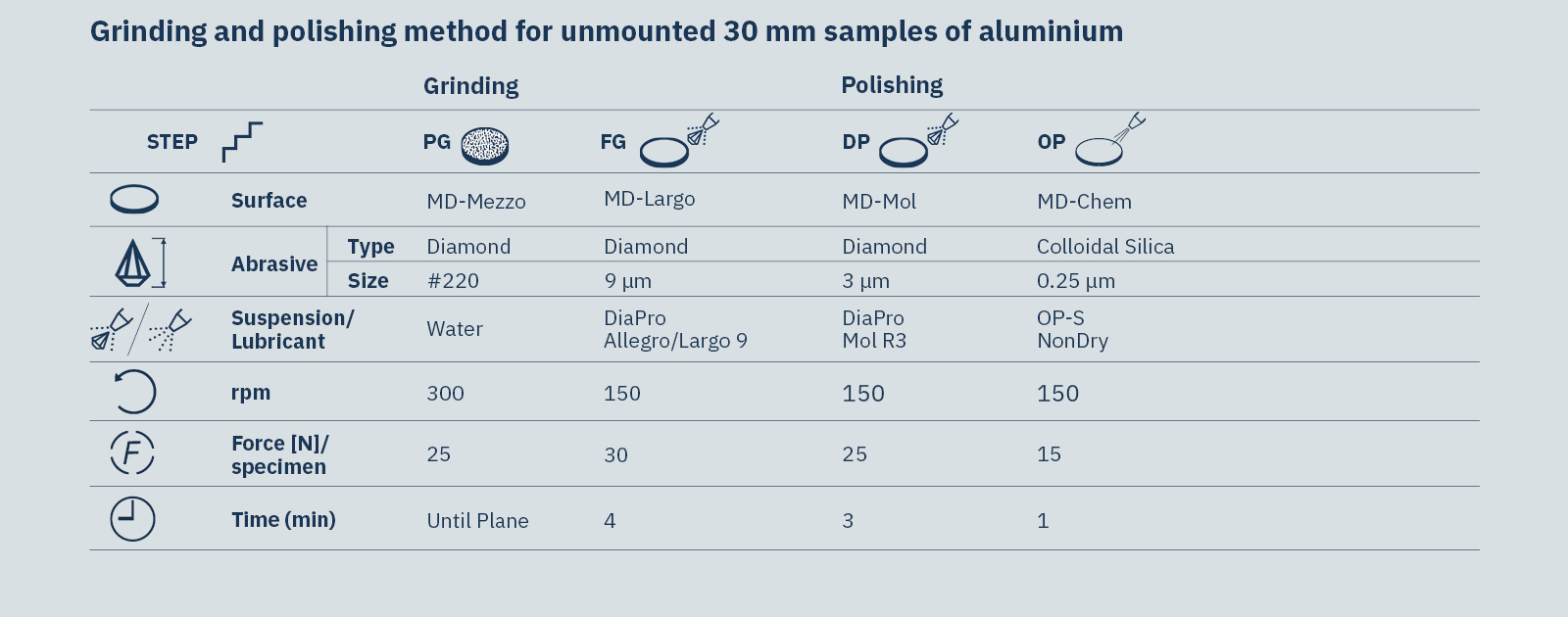
Tabella 3. Metodo di prelevigatura e lucidatura per campioni di alluminio da 30 mm. non inglobati
Per ulteriori dettagli su questa metodologia, consultare la nota applicativa completa.
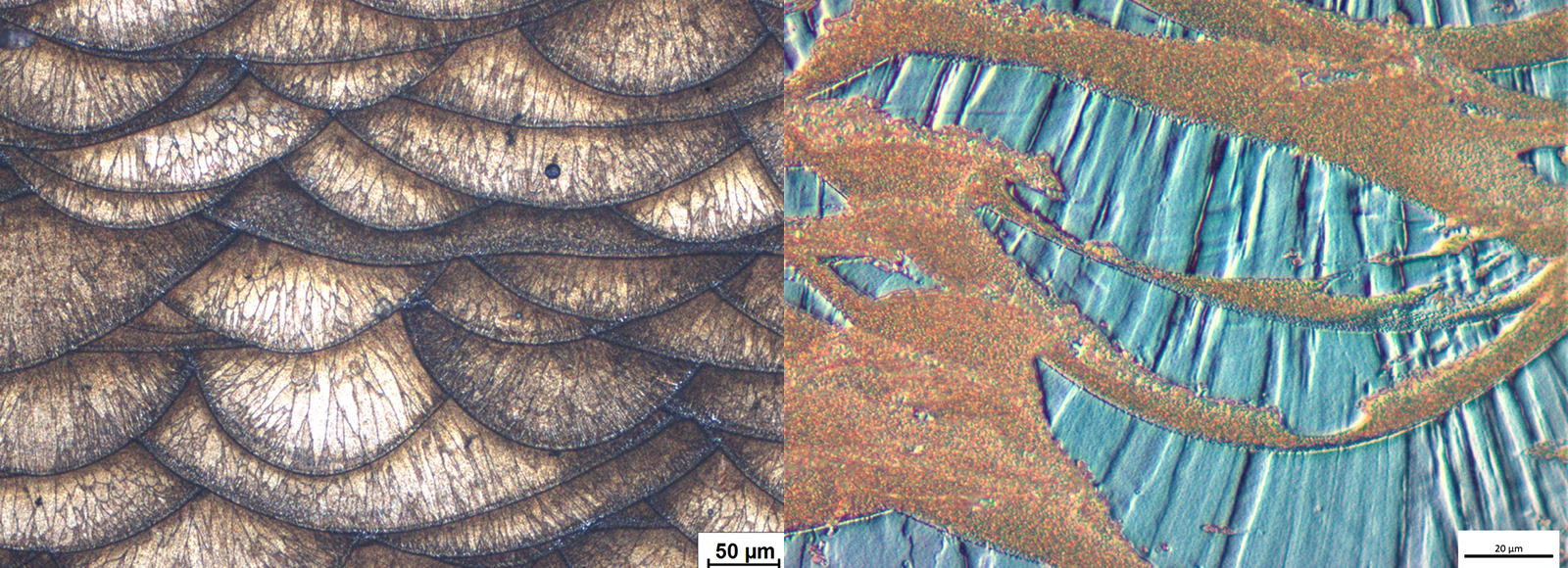
Figura 18. Leghe di alluminio diverse dopo attacco Barker in campo luminoso (a sinistra) e in contrasto interferenziale differenziale, DIC, (a destra).
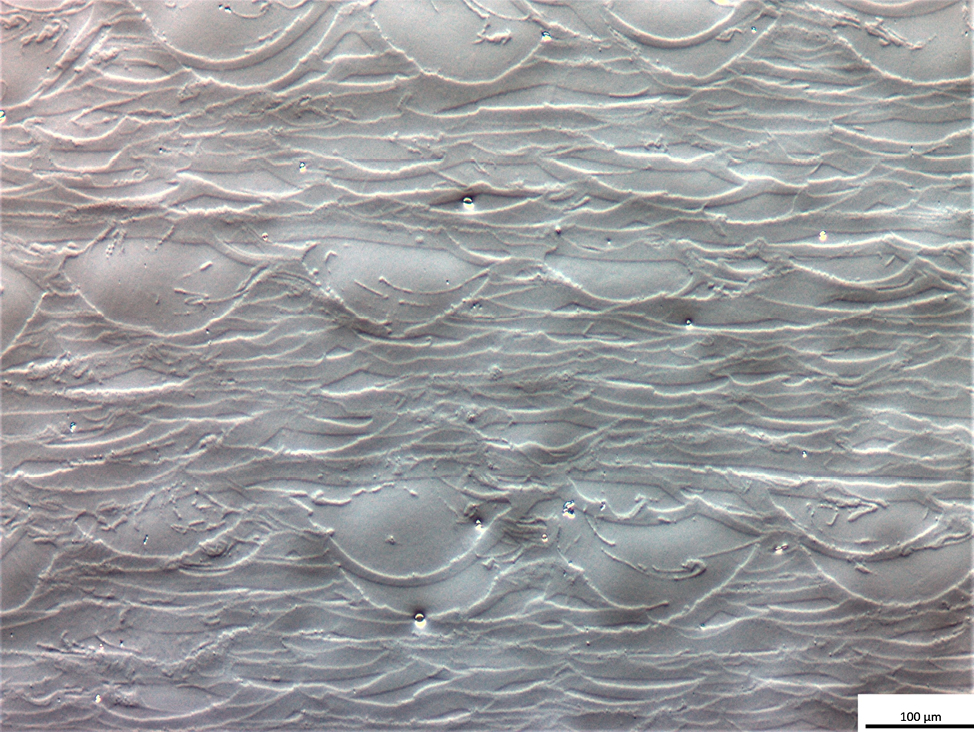
Figura 19. Superficie finemente lucidata di lega di alluminio. Lucidata con MD-Chem e OP-S. Contrasto interferenziale differenziale, DIC, senza attacco.
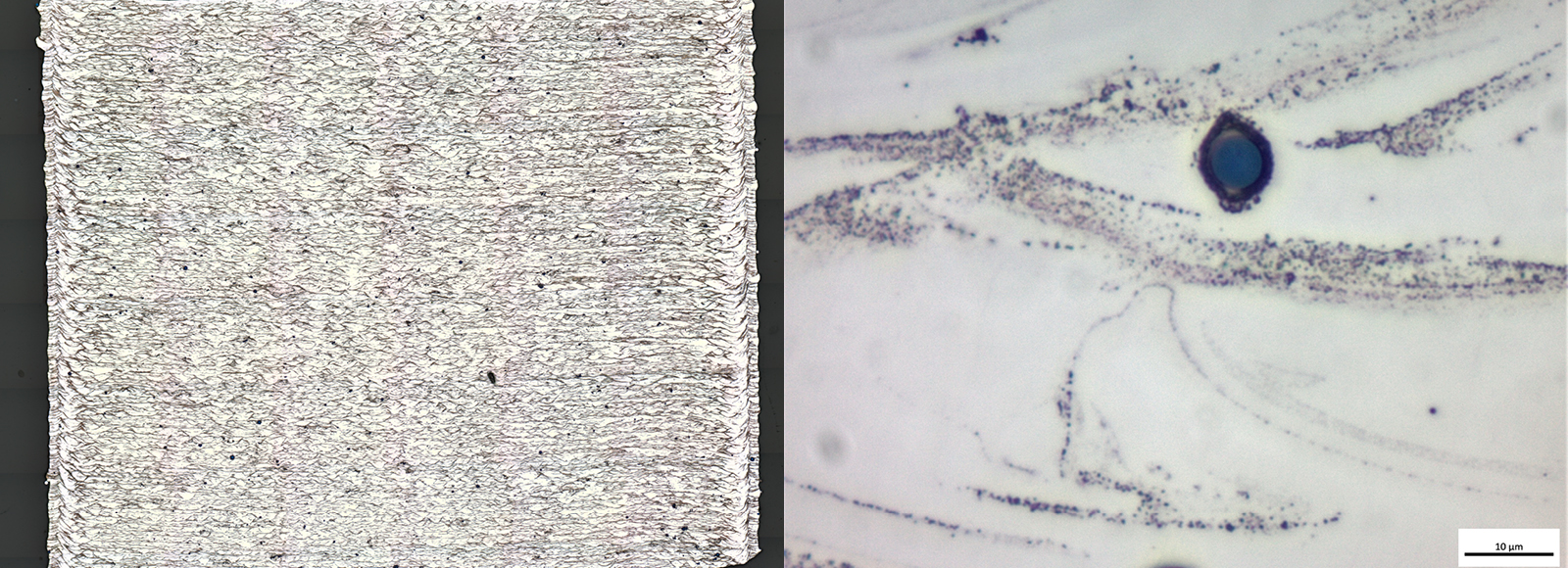
Figura 21. Visione della lega di alluminio, attacco con Barker (a sinistra). Dettaglio della lega di alluminio, con precipitazione ad alto ingrandimento (a destra). Campo luminoso.
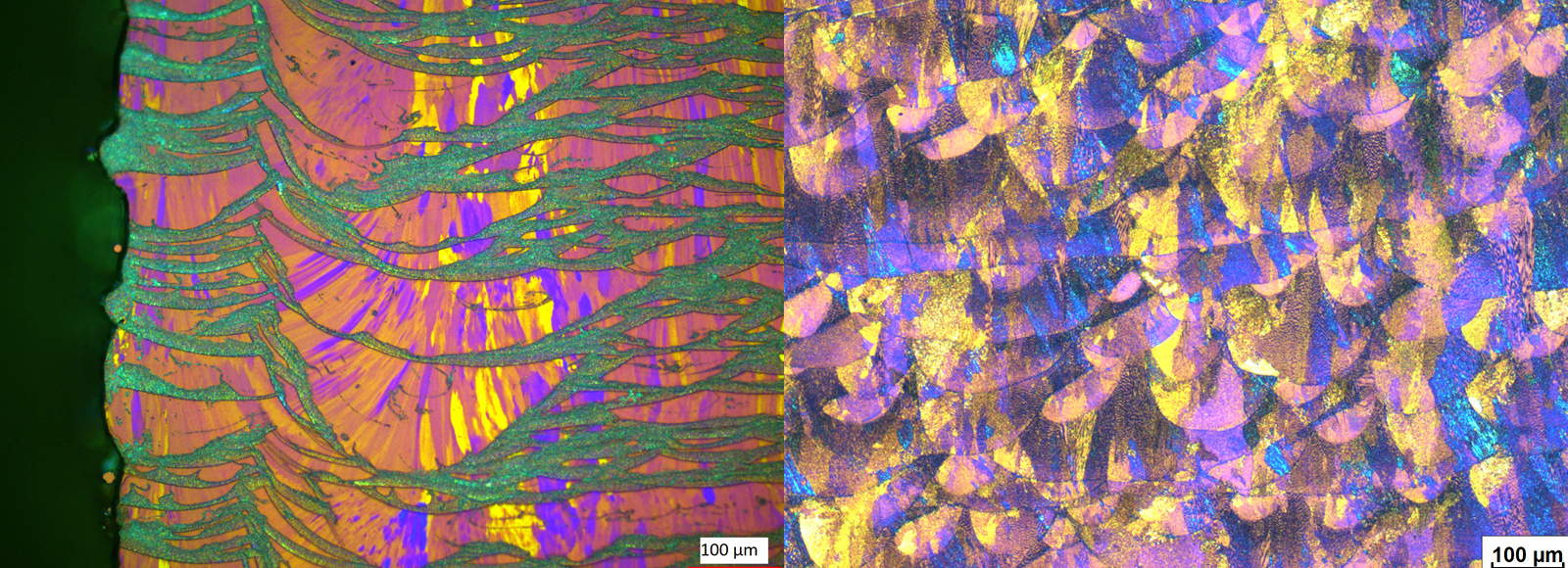
Figura 22. Lega di alluminio dopo attacco Barker (a sinistra). Inconel attaccato con Adler (a destra). Luce polarizzata. Acciai inossidabili e leghe a base di nichel Poiché questi materiali sono spesso morbidi e duttili, è opportuno evitare l'utilizzo di superfici di prelevigatura molto grossolane e l'alta pressione. In generale, la preparazione dovrebbe seguire i metodi standard utilizzati per altri acciai inossidabili e leghe a base di nichel.
- Utilizzare un disco di spianatura dedicato, come MD-Alto.
- La prelevigatura fine dovrebbe essere eseguita con sospensione diamantata su disco rigido (MD-Largo) o panno MD-Plan.
- Far seguire alla prelevigatura fine un'accurata lucidatura diamantata su un panno medio/duro (MD-Dac).
- Si consiglia una lucidatura finale con silice colloidale (OP-S) o allumina (OP-A) per rimuovere eventuali graffi superficiali.
- L'attacco elettrolitico con il 10% di acido ossalico in acqua è una pratica comune. Tuttavia, per gli acciai duplex, l'attacco elettrolitico con NaOH (20 % in acqua) offre risultati migliori.
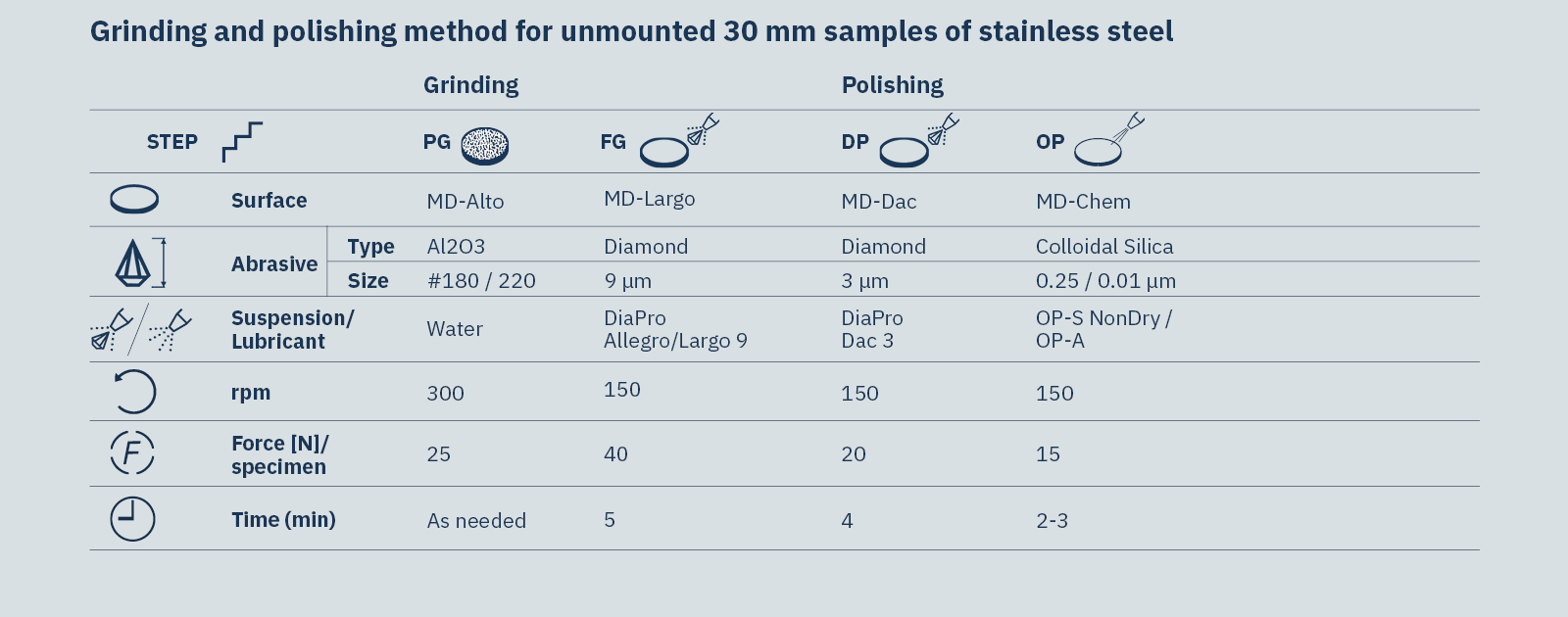
Tabella 4. Metodo di prelevigatura e lucidatura per campioni di acciaio inossidabile da 30 mm. non inglobati
Per informazioni più dettagliate su questa metodologia, inclusa la preparativa per la valutazione della porosità, consultare la nota applicativa completa.
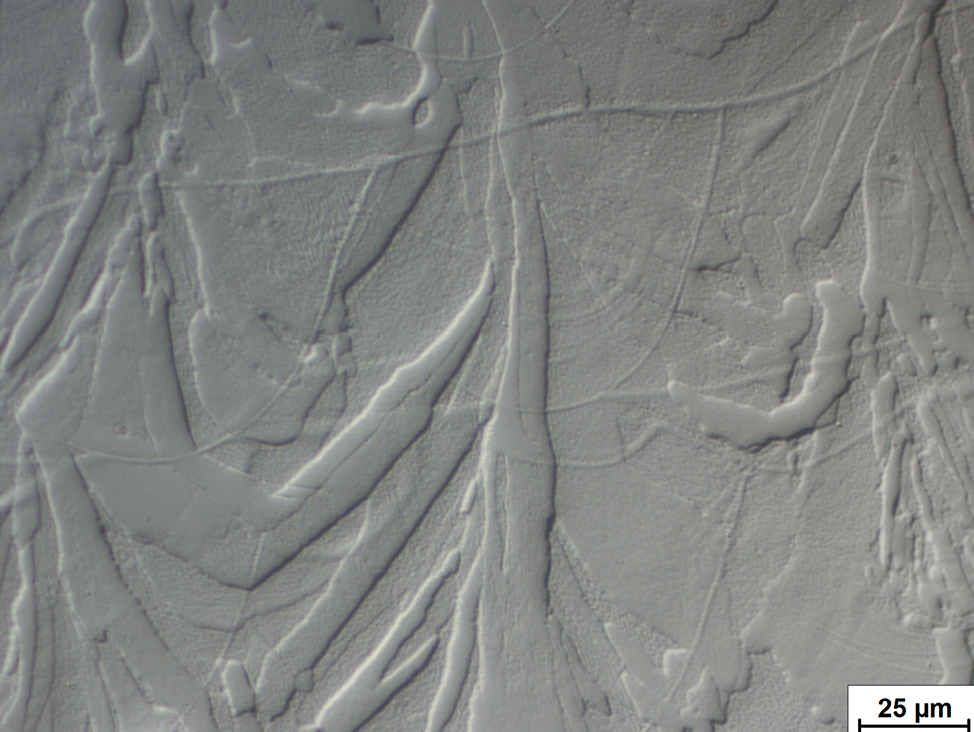
Figura 24. Acciaio austenitico dopo lucidatura con OP-S su MD-Chem. Struttura visibile senza attacco chimico. Contrasto interferenziale differenziale, DIC.
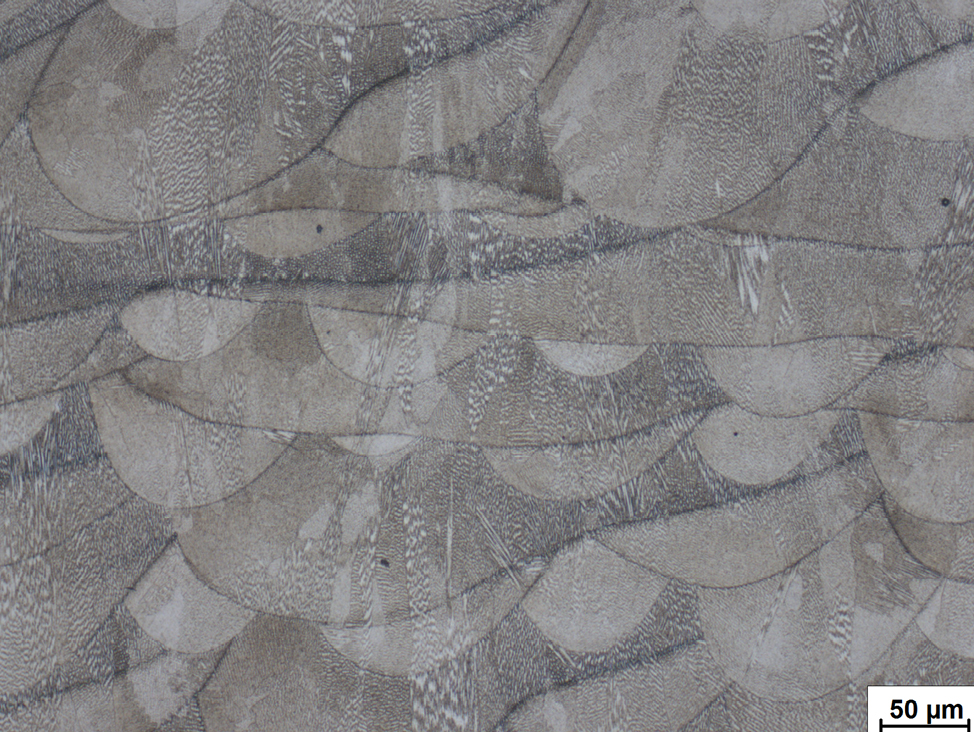
Figura 25. Inconel 718, attaccato con reagente Adler. Campo luminoso.
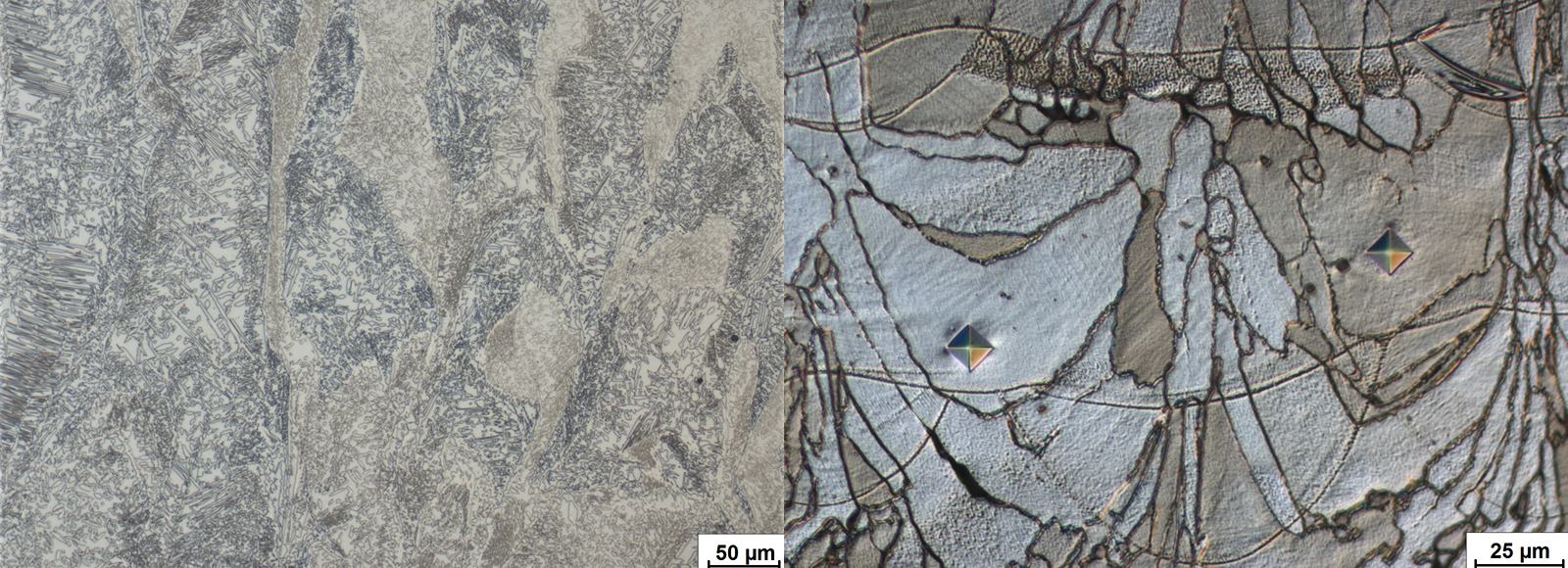
Figura 26. Acciaio duplex 1.4462 dopo attacco elettrolitico con acido ossalico (10%). Campo luminoso (a sinistra). Acciaio duplex 1.4410 con impronte di micro durezza, dopo attacco elettrolitico con NaOH 20% in acqua. Contrasto interferenziale differenziale, DIC (a destra). Acciai per utensili L'acciaio per utensili è prodotto con grandi quantità di elementi leganti come cromo, nichel, vanadio o molibdeno. La principale difficoltà durante la prelevigatura e la lucidatura consiste nel garantire la conservazione di carburi e inclusioni non metalliche. In generale, la preparazione dovrebbe seguire i metodi standard utilizzati per altri acciai per utensili.
- Per la spianatura, si consiglia di utilizzare gli appositi dischi con diamanti incorporati (MD-Piano).
- Per la prelevigatura fine, utilizzare un disco diamantato legante metallo (MD-Allegro) con sospensione diamantata.
- Per acciai altolegati è possibile utilizzare il reagente Klemm.
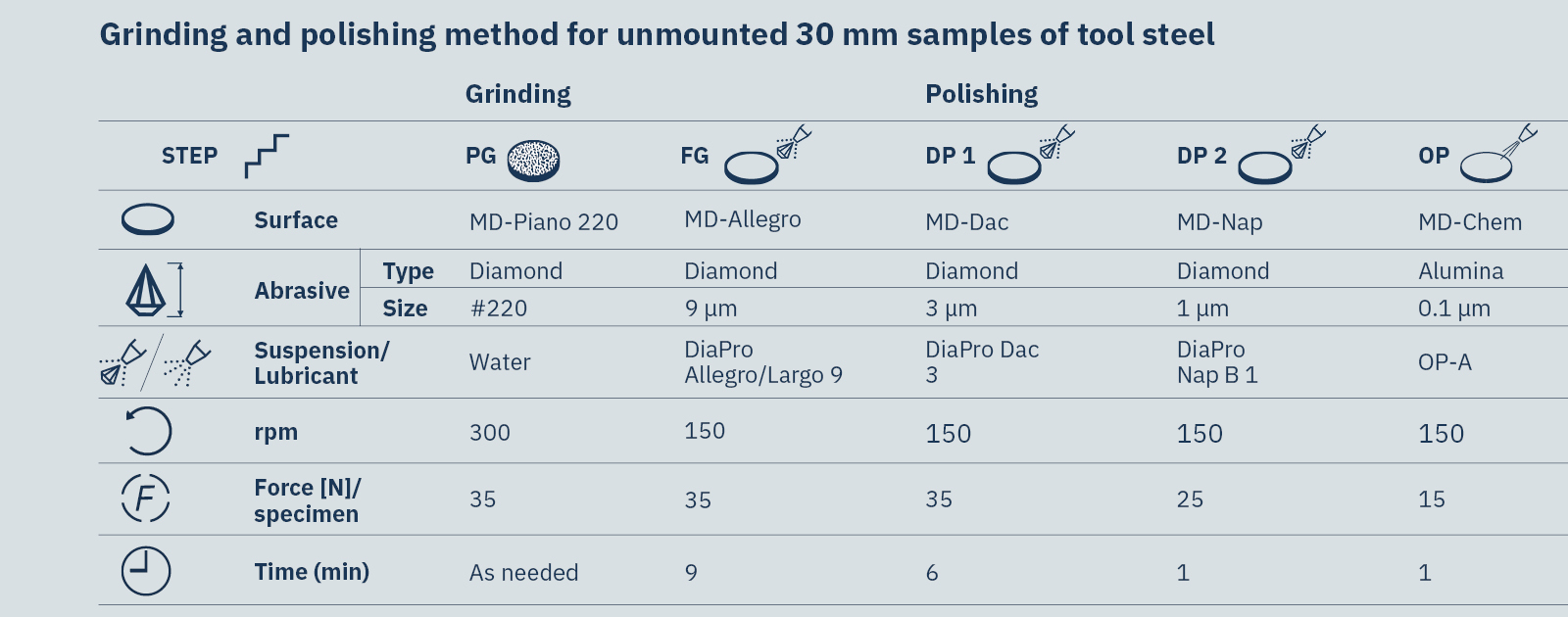
Tabella 5. Metodo di prelevigatura e lucidatura per campioni di acciao per utensili da 30 mm. non inglobati
Consultare la nota applicativa completa per informazioni più dettagliate su questa metodologia.
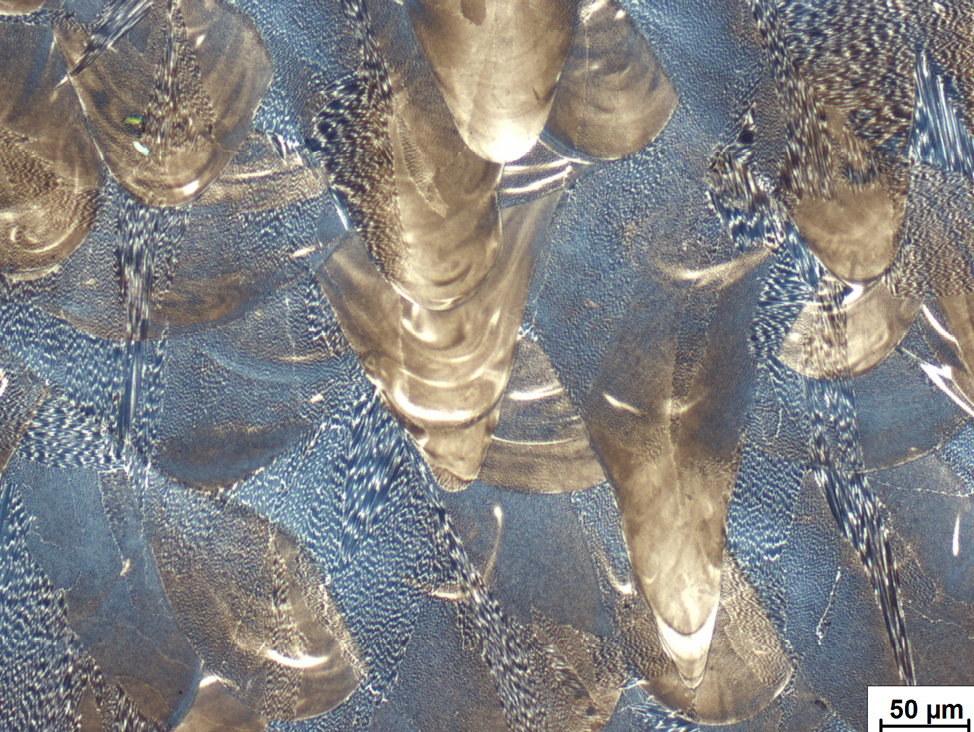
Figura 27. Acciaio per utensili 1.2709 dopo attacco con Klemm modificato (10/3) e aggiunta di HCl. Per saperne di più